随着工业制造的不断发展和市场对高质量产品的需求增长,铸造行业变得越来越重要。精铸车间作为铸造的核心环节,其生产效率、产品质量和资源利用率对企业的竞争力和发展具有重要影响。然而,传统的精铸车间存在一些问题,如生产效率低、质量控制不准确等。在这一背景下,数字孪生技术的应用为精铸车间带来了一场智能化变革,实现了对铸造的升级。
功能点:
- 实时监测与质量控制:数字孪生精铸车间通过传感器和数据采集技术,实时监测设备的运行状态和生产数据。系统可以及时捕捉铸造过程中的温度、压力、震动等关键参数,实现对产品质量的实时监控和准确控制,帮助企业提升产品质量水平。
- 智能模具设计与优化:数字孪生技术为精铸车间的模具设计和优化提供了支持。系统可以通过数字仿真技术,对模具的结构进行优化和改进,提高铸件的成形性能和生产效率。同时,系统还可以根据实时数据和算法分析,智能调整模具参数,优化生产过程,提高铸造产品的精度和一致性。
- 数据分析与工艺优化:数字孪生精铸车间借助数据分析和工艺优化技术,实现对铸造工艺的准确控制和优化。系统可以分析历史数据,发现工艺参数对产品质量和产能的影响,提供科学的工艺优化方案,帮助企业提高生产效率和产品质量。
- 资源利用与能效优化:数字孪生技术为精铸车间的资源利用和能效优化提供了支持。系统可以对热能、电能等资源的消耗进行准确监测,分析资源利用情况,帮助企业优化能源消耗,减少资源浪费,实现节能减排的目标。
- 远程运营与智能管理:数字孪生精铸车间通过远程运营和智能管理技术,实现对生产过程的远程监控和智能化管理。系统可以通过远程监控技术,实时监测设备运行状态,提供预警信息,帮助企业及时处理问题。同时,系统还具备智能管理功能,可以对生产任务进行智能调度和优化,提高生产效率和资源利用率。
数字孪生精铸车间的智能化管理助力高质量铸造,实时监测与质量控制、智能模具设计与优化、数据分析与工艺优化、资源利用与能效优化、远程运营与智能管理等功能点为精铸车间提供了智能的管理解决方案。
继续阅读
预约演示 项目咨询
扫一扫,加我就对了
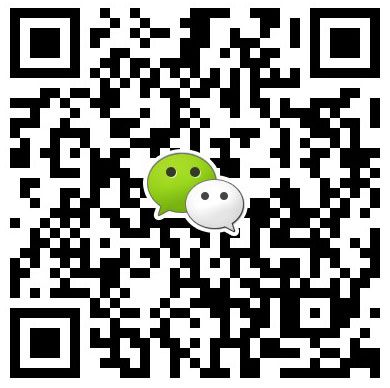
吉优赛维公众号
因为专注 所以专业
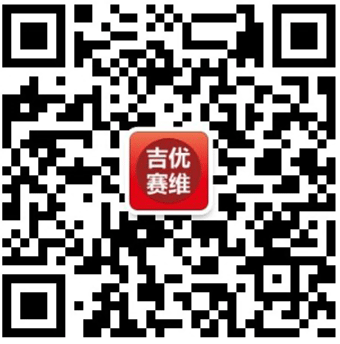
评论